Unlocking Energy Efficiency in Manufacturing with the Direktin Platform
- Elvira Rakova
- Oct 23, 2023
- 5 min read
Productivity and performance remain the primary economic drivers in the manufacturing industry, especially in a context where energy crises are becoming increasingly pressing. However, despite being seen as a secondary objective, energy efficiency can offer significant benefits that go beyond just a "nice to have" bonus.
The challenge lies in the perception that energy efficiency measures often entail difficult or uncertain changes to productivity due to potential alterations in functionality, potentially complicating a company's competitive position in the market. This challenge is particularly evident in the design of pneumatic systems, where even with new, efficient components available on the market, their integration is not yet considered an optimal practice.
This is where the Direktin platform, developed in collaboration with Artema, plays a vital role. It streamlines the implementation of energy-saving measures and facilitates the adoption of high-energy efficiency solutions, reducing prices through increased volume.
In essence, the platform presents a win-win scenario for component suppliers by promoting their energy-efficient solutions and expanding their market. The free software serves as a powerful tool for designing compressed air systems, covering various aspects, such as cylinder sizing, choice of blowing applications, tube and valve sizing, and other components.
The tool is underpinned by a growing database from Artema, established in collaboration with leading pneumatic component suppliers. Integrated energy efficiency measures are based on the research, and test validations with calculations conforming to ISO standards.
Through this platform, component suppliers can seamlessly integrate their energy-efficient solutions, delivering added value to their customers and contributing to a more sustainable and efficient industrial landscape. The platform's approach effectively bridges end users and machine builders with instrument suppliers in an environment that fosters a reduction in compressed air energy consumption in industrial applications and process optimization. This, in turn, results in improved machine performance and reduced energy consumption, allowing end users to realize significant energy savings.
caters to the needs of industrial entities keen on optimizing the energy efficiency of their compressed air systems in a safe and user-friendly manner.
How Does the Tool Work?
The software offers a component library, enabling users to select and combine components in a pneumatic diagram. Rather than following a conventional top-down approach (from the energy source to the utility), this method begins with the pressure and flow requirements at the actuator level and works its way up to the energy source to determine the required upstream airflow and pressure. Following the calculations, further energy efficiency can be achieved by utilizing the "optimization" command to replace the weakest link. This unique approach eliminates unnecessary pressure drops while meeting the needs of a machine or workshop.
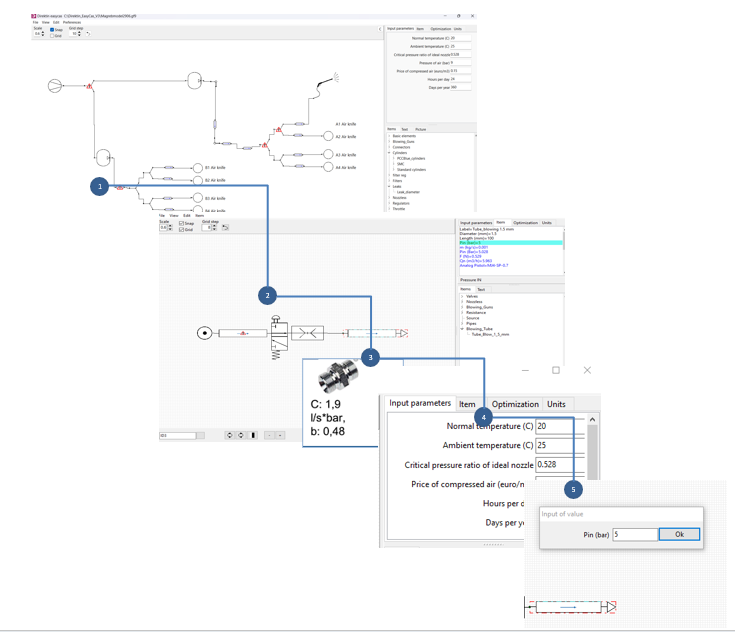
Step by step, from downstream to upstream, the software calculates the pressure and flow at the inlet of each component based on the calculated pressure and flow at its outlet, adhering to the calculation rules of ISO standard series 6358, which introduced component-specific flow characteristics, C and b:
- C, Sonic Conductance: Corresponding to the maximum flow rate (in sonic regime).
- b, Critical Pressure Ratio: Representing the boundary between sonic and subsonic flow.
A component can be a valve, fitting, hose, regulator, filter, or blowgun. Cylinder actuator calculation is also the focus of calculation.
Given the complexity of these calculations, a specialized digital tool is indispensable for identifying each component by its C and b parameters. For hoses, each section is characterized by its length, inner diameter, and material, allowing the calculation of its C and b characteristics in accordance with ISO 6358. For other components like pressure and flow regulators, their characteristic curves facilitate obtaining pressure drop data needed for circuit calculations.
By preventing oversizing, coupled with the effective management of leaks the software optimizes pneumatic systems. It is worth noting that the tool can incorporate leaks as a library component. The potential of this tool is enormous, as it not only optimizes the compressed air circuits from the design stage but also serves as a universal tool, not tied to a specific pneumatic component supplier. This database is continually expanding, as suppliers recognize the benefits of offering a shared tool for the industry.
Optimizing Energy-Hungry Applications
One of the tool's significant advantages is its capability to optimize pneumatic consumers. In the industrial sector, compressed air applications such as blowing are widely used for cleaning, cooling, and transport, as well as actuators. Approximately 10% of industrial energy in Europe is consumed in producing compressed air, with 20% used by actuators and about 5% by pneumatic tools. Unfortunately, 15% of this energy is lost due to leaks. The most extensive use of compressed air, roughly 50%, is for compressed air blowing and actuation.
A step-by-step application and component selection from the database can save time in designing and maintaining pneumatic systems by avoiding technical issues and reliance on traditional catalogs. Importantly, any component change impacts the entire network and should be considered accordingly.
Optimization Process
To start optimizing or designing a new compressed air system, users create a diagram using a standard component library and components from various suppliers. The components have catalog parameters, such as hose diameter, that are both entered and calculated. Unlike other tools where each component needs individual parameterization, here, users simply choose from an online catalog within the program. After completing the diagram, users input general information, including the cost of compressed air, system operating hours, annual operating days, and ambient temperature. It's also crucial to enter the maximum allowable pressure drop for optimization.

Upon clicking "calculate," the program provides information on system pressure losses, flow rates, compressed air consumption, costs, and the pressure level required at the regulator or pressure source for proper system operation.
Optimization Algorithms
Optimization algorithms identify the most restrictive components with the highest pressure losses and provide suggestions for improvement. For hoses, it suggests optimal parameters, and for valves, it recommends optimal characteristics such as sonic conductance or flow. This principle extends to other component types.
Consumer Improvements
Regarding blowgun tubes, the tool calculates blowing force and flow and suggests suitable blowgun nozzles or guns from the catalog that meet requirements. The energy savings typically reach around 50%, accompanied by enhanced safety and reduced noise levels. In the case of cylinder application, it calculates the diameters, velocities, and other physical parameters.

Tool as an Energy Efficiency Benchmark
Another notable feature of this tool is its capacity to assess the energy efficiency of an operational pneumatic solution. For instance, it enables the neutral communication of energy efficiency information about a machine's compressed air circuit based on ISO standards.
The tool remains continually updated with new calculations and components, including cylinder selection and energy-saving measures, vacuum technology (coming soon), and more. The database, under constant expansion, provides a comprehensive overview of the pneumatic market and allows for the integration of specific components. The program is free and simplifies pneumatic system optimization in just a few clicks.
This tool has the potential to revolutionize the perception of compressed air. It is user-friendly and, more importantly, provides responses tailored to the energy requirements of the industrial world. Over time, it could become a benchmark for monitoring and can be easily connected to sensors becoming a full SCADA system.
Comments